High Entropy Alloys for coatings materials characterized by increased erosion resistance in different applications.
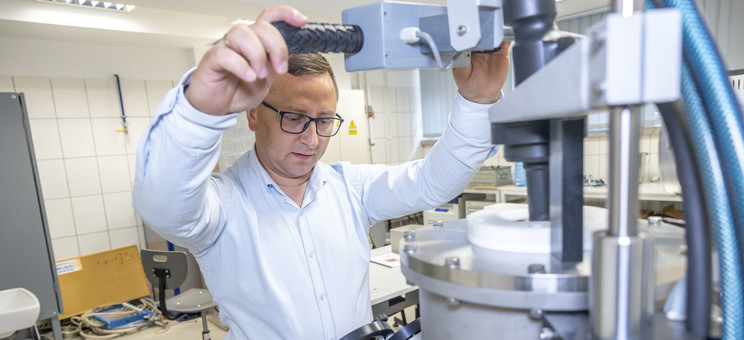
Project is performed within the VIA CARPATIA Polytechnic Network ointhe name of the President of the Republic of Poland Lech Kaczyński. The project manager is D.Sc. Wojciech Nowak, Associated Professor from the Department of Materials Science at the Faculty of Mechanical Engineering and Aviation of the Rzeszów University of Technology. The research project is carried out by a cooperation of three research groups: research team from the Białystok University of Technology, the Lublin University of Technology and the Rzeszów University of Technology. The project leader is the Rzeszów University of Technology.
Research team
Bialystok Technical University: Principal Investigator: D.Sc. Małgorzata Grądzka-Dahlke, Associated Professor PB, Research team members: D.Sc. Dariusz Perkowski, Associated Professor PB, Marzena Tokarewicz, M.Sc.
Lublin University of Technology: Principal Investigator: D.Sc. Mariusz Walczak, Associated Prof. PL, Performers: Mirosław Szala, Ph.D. Eng.
Rzeszow University of Technology: Shareholders: D.Sc. Wojciech J. Nowak, Associated Prof. PRz, Performers: Tadeusz Kubaszek, Ph.D. Eng., Andrzej Gradzik, Ph.D. Eng.
Project description
Metallic materials constitute a group of basic construction materials, because of their excellent strength properties and the anisotropic nature of their properties, as well as the possibility of their application in the form of a coating. Metallic materials that are obsolete are very often used in conditions that expose these materials to abrasive and erosive conditions. Their degradation may occur according to different mechanisms. Materials used for cutting tools or functional elements degrade due to the tribological effect. In turn, metallic materials used in engines can be damaged by erosion due to collision with flying ash particles at high temperature. Examples here may include induction of volcanic ash in the air or sand dust, and erosion of gas turbines blades. Erosion processes can also occur at high temperatures, as in the case of dust, which is a spalling oxide scale, entering the combustion chamber or high-temperature turbine. In turn, traces from which elements used to transport fluids (cold or hot water, fuel, or steam) are made are the result of cavitation and degradation as a result of cavitation erosion. Thus, it is necessary to increase the abrasion resistance of the elements by, e.g. developing new abrasion resistant alloys or applying protective anti-abrasive coatings or layers.
The modern technologies used for manufacturing of coatings resistant to friction and erosion damage are e.g. laser cladding or plasma spraying. Materials used nowadays for coatings are usually nickel- or cobalt-base superalloys, composites, or ceramic materials. There are no alloys on the commercial market that demonstrate applications in which friction resistance under different operating conditions, especially in the case of synergistic tribological effects. High-entropy alloys (HEA) seem to be a promising candidate. They constitute a developing group of materials. High-entropy alloys (HEAs) consist of at least five near-equiatomic elements. Each main element should be doped with 5 to 35 at%. In addition to the element, HEA can be doped by other elements, but their total amount should be less than 5 at%.
However, the largest application of HEA alloys to date is in applications in corrosive conditions. The number of scientific works on the assessment of the microstructure of HEA alloys is systematically increasing, but there is no work focusing on the simultaneous assessment of abrasive wear resistance,, cavitation erosion resistance and resistance to erosion by solid particles assessed at room and elevated temperatures. HEA alloys enable modification of the chemical composition while maintaining the stability of their microstructure, and thus it is highly probable to obtain materials with the desired wear resistance in various operating conditions. This statement is supported by the results of the project team's own research. Therefore, as part of this project, high-entropy alloys (HEA) are proposed as a material used to produce coatings that increase resistance to abrasive and erosive wear. A modern and economically justified approach is to produce protective coatings on available materials rather than producing complete components from new materials. However, depending on the manufacturing method, coatings may have serious limitations. Plasma-sprayed coatings exhibit high porosity, poor adhesion to the substrate, and heterogeneous microstructure. In turn, coatings produced using a laser ensure high adhesion to the substrate. Therefore, in this project, the coatings will be produced using plasma and laser methods.
An appropriately selected research program to understand the characteristics of resistance to abrasive wear, erosion by solid particles, and cavitation erosion will therefore contribute to predicting the properties, design, and practical applications of HEA materials. This is especially true since the development of HEA alloys in the original chemical composition is planned, previously unavailable in the literature. The analysis of literature data and the authors' own research of the project indicate that the research topic seems current and fully justified. Due to the above, the following project goal was formulated: Development and production of coatings from an original high-entropy alloy characterized by increased wear resistance under various operating conditions.
The research leading to these results has received funding from the commissioned task entitled “VIA CARPATIA Universities of Technology Network named after the President of the Republic of Poland Lech Kaczyński” contract no. MEiN/2022/DPI/2578 action entitled “ISKRA – building inter-university research teams”.