Mineral composites as a component of dura, safe asphalt pavements that reduce negative environmental impacts
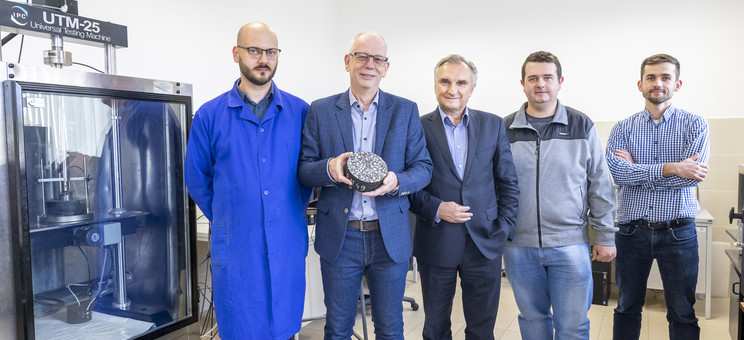
Project is performed within the VIA CARPATIA Polytechnic Network ointhe name of the President of the Republic of Poland Lech Kaczyński. The project manager is Prof.Tit. Tomasz Siwowski from Department of Roads and Bridges at The Faculty of Civil and Environmental Engineering and Architecture of the Rzeszów University of Technology. The research project is carried out by a cooperation of three research groups: research team from the Białystok University of Technology, the Lublin University of Technology and the Rzeszów University of Technology. The project leader is the Rzeszów University of Technology.
Research team
Bialystok Technical University: Principal Investigator: Władysław Gardziejczyk, BEng, PhD, DSc, ProfTit., Research team members: Marta Wasilewska, BEng, PhD, Paweł Gierasimiuk BEng, PhD
Lublin University of Technology: Principal Investigator: Agnieszka Woszuk, BEng, PhD, Research team members: Szymon Malinowski, PhD, Michał Wróbel BEng, MSc. (PhD student)
Rzeszow University of Technology: Principal Investigator: Tomasz Siwowski, BEng, PhD, DSc, ProfTit., Research team members: Lesław Bichajło, BEng, PhD, Krzysztof Kołodziej, BEng, PhD
Project description
The aim of the project is to establish optimum solutions for selected mineral-asphalt mixtures based on mineral composites produced at reduced technological temperature. The mixtures developed should guarantee the durability of road and bridge pavement layers, provide good anti-slip properties and contribute to reducing the negative impact on the environment. Currently, the production of mineral and asphalt mixtures using conventional technologies (HMA – hot mix asphalt) takes place at high temperatures of up to 230°C.
In order to minimise the negative impact on the environment, it is important to optimise the selection of environmentally-friendly asphalt mixture production technologies, such as warm mix asphalt (WMA), which, among other things, reduces fuel consumption and the emission of harmful fumes and aerosols into the atmosphere. Reducing process temperatures can be achieved, among other things, by adding minerals from the zeolite group. The crystalline structure of these minerals contains chambers and channels of different dimensions, which make it possible to store water or other polar compounds. This specific type of structure gives them many physical and chemical characteristics, including the ability to absorb small molecules of compounds. Due to the functional structure of the material, it is also possible to introduce external water into the zeolite structure, which intensifies the foaming process of the asphalt.
The project involves the modification of zeolites with compounds from the silane group containing different amounts of sulphur, which have not yet been described in the literature. The scope of the research work envisaged in the proposal also includes an analysis of the water and frost resistance of modified asphalt binders based on surface free energy (SEP) measurements, taking into account different conditioning conditions (pressure, temperature, presence of water) of the samples. This approach to the indirect determination of the frost resistance of asphalt binders has not yet been analysed. The application of the obtained mineral composites to special-purpose asphalt mixtures, i.e. poured asphalt for pavements on bridges, SMA LA in wearing courses for road noise reduction, will be of significant scientific value.
The wearing layer should be durable and ensure driving comfort, user safety and reduce the negative environmental impact of transport. This is possible through the right choice of materials and the composition of the asphalt mixture. The traditionally built SMA asphalt wearing course for roads with traffic categories KR4-KR7 is a durable solution. However, the problem of aquaplaning remains, which limits the generation of frictional force at the tyre-surface interface in sliding conditions, and the rolling noise level of motor vehicles generated at the tyre-surface interface is higher than with porous asphalt layers. Porous asphalt layers, on the other hand, do not provide satisfactory durability, especially in countries with negative winter temperatures. Keeping in mind the need to reduce vehicle rolling noise and aquaplaning, a mastic-grit SMA LA mix is designed as an intermediate solution between SMA mix and porous asphalt. Like the SMA mix, the SMA LA mix should be designed on the basis of polymer-modified asphalts. The free-space content (at least 10-12%) and the high coarse aggregate content (approximately 80%) contribute to the ‘openness’ of the structure and the ‘negative’ texture of the layer made of SMA LA mix. This contributes to a reduction in noise at the tyre/road interface and faster drainage at the tyre/surface interface of SMA LA.
In Poland, the SMA LA mixture is not widely used in the construction of wearing courses. Noise tests on SMA LA pavements built in Germany, Denmark and Belgium have shown that they reduce vehicle rolling noise by approx. 2.0 dB compared to a reference pavement made of SMA grit mastic. This was also confirmed by a study carried out by a team from the Bialystok University of Technology on the S51 expressway. The state of the art in the field of SMA LA mixes research indicates that so far the main focus has been on testing polymerasphalt-based mixes. The implementation of the project from the point of view of the use of mineral composites will make it possible to identify a new technological solution beneficial from the point of view of durability, anti-skid and acoustic properties in the SMA LA mixture. There is no information in the literature on the production of SMA LA mixtures at reduced technological temperature. It is therefore necessary to carry out a detailed study of SMA LA mixes to determine the effect of their composition on durability, anti-slip and acoustic properties.
The poured asphalt mixture has a very high tightness (void content of about 1-1.5%), which predestines it for use in pavement layers on bridges as a protective layer of insulation. The properties of the cast asphalt protective layer provide a good barrier to water, so it is considered complementary to bridge insulation. It is produced at a higher temperature (more than 200°C) than classic rolled mixtures (about 180°C), which creates additional requirements for the bridge deck insulation on which the protective layer is spread. In performance practice in Poland, the inadequate resistance of the insulation to the elevated temperature, manifested by blistering and bulging of the pavement, has been found on more than one occasion. At the same time, due to the reduced proportion of coarse aggregate fractions in the mix, poured asphalt may have a lower resistance to permanent deformation than layers made from rolled mixtures.
Research has been carried out at the Rzeszów University of Technology into the influence of the natural asphalt additive Trinidad Epure on the properties of both the binder and the poured asphalt mixture obtained with it, intended for the protective layer in bridge pavements. Studies have shown a positive effect of the additive in terms of increasing resistance to permanent deformation. It is therefore also possible to influence the resistance to permanent deformation by using a properly composed modern binder. There are no research results in the literature on the use of mineral composites with zeolites as an additive to cast asphalt to reduce process temperatures during the production and installation of such a mix. The benefit of using the innovative binder developed under the grant in a poured asphalt mix could be to reduce the risk of making a defective pavement on bridges, as well as to achieve a longer pavement life while reducing energy consumption for the production and incorporation of the poured asphalt mix on bridges. This means achieving an environmental effect.